ATV's tests of aerial poles / masts
Also see Brackets and galvanising on test
Subject list :
- Background to the tests incl :
- - Definition of pole failure
- Straight poles test results
- Cranked poles test results
- Mast test stress data
- How strong are scaffold poles ?
- Seam welded v extruded alloy poles
- Plate mount / satellite mount on test
- How strong is 20mm x 20mm x 2.0mm box section alloy ?
Also see :
- Actual aerial arrays : pole strengths
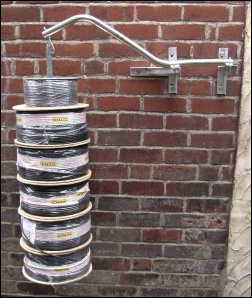
Background to these pole tests
Well, back in Apr 2008 we finally got round to it, and tested most of the aerial poles on the market.
These aren’t meant to be super accurate tests, they’re just to give an idea which poles are the strongest (and how strong they are relative to each other) because nobody in the aerial trade actually knew when we asked them. The answers were all prefaced by “we think that….”, ‘we’re told that…..,’ or (most candidly) “we don’t actually know.…”
We set up a test rig on our back wall and just added weights on the end of the poles till they failed. It was very interesting testing them all to destruction, in fact it was probably the most fun you can have with your clothes on.
Generally, in terms of strength, the masts failed in the order one would expect, see table, but in order to make sense of the results it is important to understand a few points :
1 - Obviously as the pole gets longer it gets weaker, as an example the 6ft x 1.25” x 16G pole failed at 25Kg but the 3ft length needed 62.5Kg to break it. Of the poles we stock only one (the 6ft x 1.0" x 1.2mm) is not a heavy duty product, but the 33" version of the same diameter and wall thickness is.
2 - What counts is the free / unsupported length of the pole, i.e. deducting the length covered by the bracket. This can be significant. For the tests of the 3ft and 6ft poles the T & Ks were 11” apart, but when we put the 10ft poles on we widened them to 20” (to outsides). This is necessary to prevent putting too much strain on the brackets, or the brickwork.... Thus the unsupported length on the 3ft poles was actually only 2ft 1”, on the 6fts it was 5ft 1” and on the 10fts it was 8ft 4in.
3 - It isn’t just about pole diameter, the gauge / thickness * of the metal is just as important. As an example a 6 foot x 1.25” x 18G pole failed at only 17.5Kg, but the thicker 16G version didn’t collapse until 25Kg, and that’s a big difference.
* Cross sectional area of 1.25” (32mm) poles of various gauges
The strength of a pole / mast is dependent on its cross sectional area, and these calculations show just how big an effect the wall thickness / gauge has on the cross sectional area.
It is also worth remembering that an alloy pole does not corrode and therefore does not lose any of its cross sectional area over time. All steel poles corrode though a hot dip galvanised one will last decades before losing significant strength, or indeed rusting much at all. Unfortunately nearly all steel masting is Pregalv whose anti corrosion performance is much less impressive, it is so ubiquitous because it is much cheaper to manufacture.
1.6mm wall thickness (16 gauge) = 153 sq mm
1.2mm wall thickness (18 gauge) = 116 sq mm
0.9mm wall thickness (20 gauge) = 88 sq mm (also equals a 1.2mm steel pole after 0.3mm of corrosion)
0.6mm wall thickness (24 gauge) = 59 sq mm (equals a 0.9mm steel pole after 0.3mm of corrosion)
It is important to define a “FAIL” in these tests. I define failure as the point the pole would keep on bending till it was L shaped. This is generally because the tubing has kinked. It must be remembered that before (this definition of) failure is reached the pole has already passed the point where it will “return to perfectly straight” when the load is removed.
As expected all poles failed right above the top bracket clamp point, that's where the pole is obviously under maximum stress. As an interesting sidelight, if you ever have a pole with a "dint" in the side, even quite a deep one, it is never going to fail there unless the "dint" is exactly at the point of the top bracket clamp*. And if it's a straight pole that would never be the case anyway because you could just use the pole round the other way !
* A pole will never fail below the top mount (i.e. between the two support points of the bracket) even if very badly dented.
Test of a 6ft x 1.6mm x 1.25" pole
v
a "Screwfix special" 6ft x1.2mm x 1"
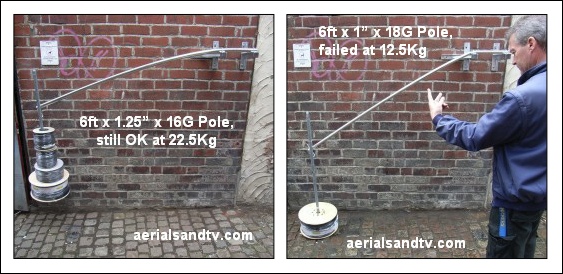
As expected the 6ft x 1” x 18G (“Screwfix Special”) were the weakest, any installer who uses this mast should be called Bertie (as in bodger). I was surprised that the 1” the steel poles weren’t actually that much stronger than the 1” alloy abominations. The 1.25” x 18G pole is worth having over the 1”, but the 16G version is much stronger. We did expect the 1.25” steel pole to be the strongest of the 6ft poles but we didn’t think that it’s superiority over the 1.25” x 16G alloy pole would be so small. Remember that the steel pole will start to weaken as it rusts. The 10 foot x 1.5” pole lasted longer than I thought it would, but it certainly flexes a hell of a lot which is why we only recommend them for aerial up to the size of a Yagi 18.
We don’t actually stock 1.5” poles at 6ft, or 2” x 14G at 10ft, but we do supply 5ft x 1.5” and 8ft x 2.0” x 14G masts, we classify them as satellite poles. We included the tests of this particular length of pole (at the 6ft and 10ft lengths) for the sake of comparison, that and we’d probably be unable to break the shorter 5ft and 8 ft versions ones without bending the T & Ks, or pulling the brickwork apart......
Tale of destruction
A 6ft x 1.25” x 16G pole tested to failure, great fun.....
It eventually collapsed at 25Kg loading, that’s 55lbs, on the end of a 6ft pole. And that’s strong !
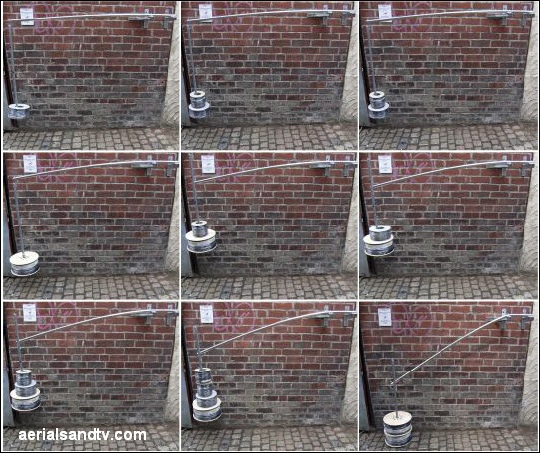

To put the above results into perspective I would call a 6ft x 1.25" x 1.6mm alloy pole "heavy duty" (and my definition of heavy duty does actually mean something). Anyway the latter pole failed at 25Kg.
The aluminium alloy poles are seam welded (5251 grade or similar), the steel poles are mild steel.
Of particular interest here is the fact that at 6ft the steel poles seem relatively stronger whereas at 10ft the alloy poles seem relatively stronger, how does that work ? (I don’t know, I’m asking you ! ) Incidentally I’d have expected the 6ft x 2in x 14G alloy poles to take more weight than they did (we tested three of them ! ), maybe the specification of the alloy was different or the gauge on the sample was slightly down, but it was still the strongest 6ft pole, which is what one would expect. To be frank wholesalers rarely quote the specifications of the alloy poles one buys from them, and, in fact, if you ask what the spec is they often don’t even know themselves, and even if they could find out some of them give the distinct impression they think you’re just being awkward asking the question ! Having said all of this, there are a number of inconsistent results which cannot be down to differing wall thickness or grade of metal because the same pole was used for the 10ft and the 6ft test. The poles were were tested at 10ft then the straight bits cut off and then tested at 6ft ! These were the 1.25in x 16G steel, 1.25in x 14G steel and 1.5in x 16G alloy, and were some of the most unfathomable results !
There was an interesting addition to the results in 2015, the 6ft x 1.25in x 20G/0.9mm steel pole. I saw a 6ft pole on E Bay and couldn’t understand how it could be sold for such a low price, even allowing for the fact it was a cheaper pre galv steel job. I ordered one expecting a 1.25in x 16G/1.2mm pole to turn up because the seller didn’t state the wall thickness (a bit naughty of him really) and 16G was the thinnest pole I thought existed at that time. Oh no, it was even thinner, I reckon it was 20 gauge (0.9mm) ! So that’s how they sell stuff so cheap….. The fact it was so thin, and a steel pole, means that, in addition to its relative weakness, any rust will have an effect on the pole’s strength rather sooner than with a thicker gauge mast.
Well look on the bright side, at least we’ve now got the full set of results for 1.25in steel poles ! :
Wall thickness / Failure load
0.9mm = 20Kg
1.2mm = 27.5Kg
1.6mm = 37.5Kg
2.0mm = 52.5Kg
On the subject of pole strengths v gauge v wind loading see these articles.
Pole strength tests, and that’s putting a hell of a lot of strain on the brackets....
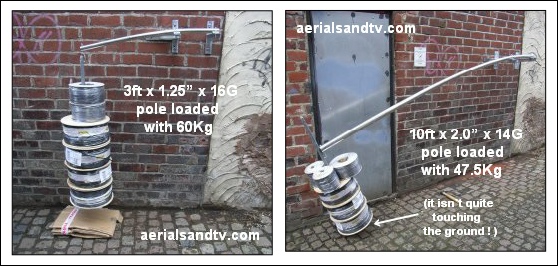
I must confess to some surprise that the cranked alloy poles weren’t actually any weaker than the straight versions, in fact the 3ft cranks were actually stronger than the three foot straights ! However it should be borne in mind that we could only test the cranked poles in one direction. Testing them with a sideways "twisting" force would just have rotated the pole in its clamps. That said, I suppose one also has to bear in mind a bit of geometry, the distance from the support, to the point at which the force is being exerted, is shorter on a cranked pole.
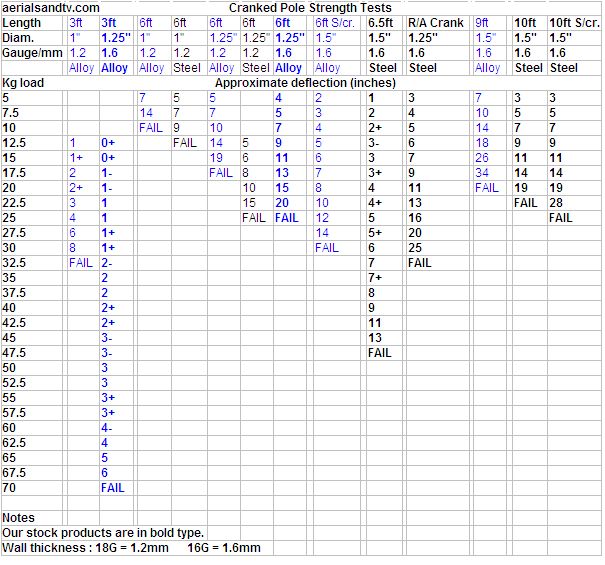
To put the above results into perspective I would call a 6ft x 1.25" x 1.6mm cranked alloy pole "heavy duty" (and my definition of heavy duty does actually mean something). Anyway the latter pole failed at 25Kg.
Note how the 10ft steel 1.5in cranks are stronger than the shorter 9ft alloy 1.5in cranks (which we used to stock), cutting a foot of the former poles would obviously make them stronger still. Bear in mind that the 10ft steel cranks are actually about the same strength as a “heavy duty” 6ft x 1.25in x 16G crank.
The 3ft x 1.25” x 1.6mm (16G) cranked pole was the strongest of all those under test. We were actually about to give up because it was getting dangerous trying to lift that much weight onto the test hook, particularly if it failed and fell on your foot ! Unlike the other poles, which kinked at the top bracket, this pole actually pulled the alloy apart, as in the picture.
The heaviest load we had to use whilst testing poles, don't drop it on your foot is all I would say.
However some explanation is required here. the 3ft x 1.25" x 1.65mm crank pole required the largest load to break it but, counter intuitively, that doesn’t necessarily make it the strongest because it it is bending force (that's force x distance) which breaks the pole and this was also the shortest pole.....
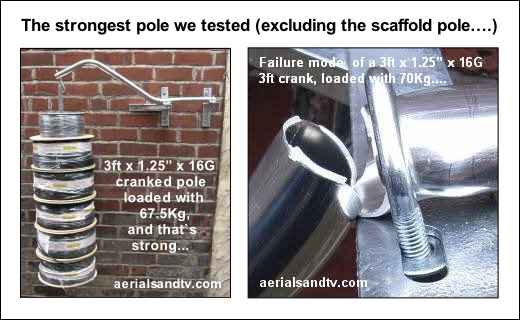
We also tested an ungalvanised 10ft crank against a hot dip galvanised one. As expected there was no difference in strength. This is because the temperature of the molten Zinc (into which the items being galvanised are submerged) is too low to have any annealing effect on the steel.
Mast test stress data
Customer research / feedback :
I am a retired mechanical engineer and I have been looking all over the web for data on the strength of antenna masts for a presentation to my ham radio club and found nothing published (even though it is important) until I discovered your test data. Thank you for doing that testing! I figured I could put your data into a spreadsheet and calculate the maximum bending stress in the mast. I took the maximum unfailed (excluding where the mounting brackets failed) as the failure point and also estimated the yield point where the force-deflection curve moved away from linear. Thanks, Steve McKeown
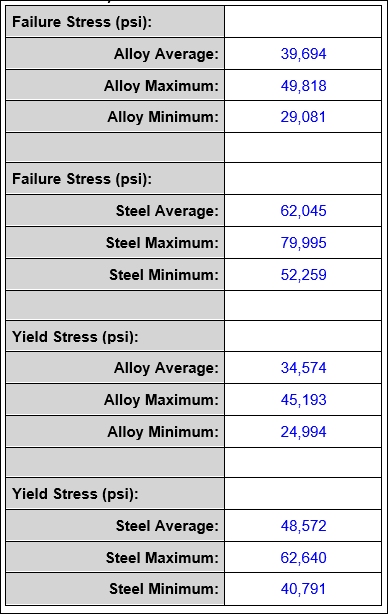
How strong are scaffold poles ?
Scaffold poles (aluminium ones) are expensive, and fairly heavy, and hard to get hold of, but they should be pretty strong as their wall thickness is 4.0mm. We decided to stock them in 2018 because they are handy if guy wiring the pole is impractical, not only are they strong but they don’t flex as much as a two inch by 2.0mm wall thickness pole, the latter being pretty strong it must be said. As an aside scaffold poles are not quite 2 inches in diameter, they’re actually 48.3mm though our 2" pole couplers still fit them. Anyway, we thought we’d compare the strength of a 3.6m (approx 12ft) scaffold pole with a 3.6m by 2” by 2.0mm pole. The 3.6m x 2” pole failed at 37.5Kg, that is impressive actually, think about it that’s 37.5Kg on the end of a (free length) pole of 10ft 7”, think about the forces there….. We were unable to test the scaffold pole to destruction because the load was touching the floor before the thing failed. This was partly because the test brackets were being bent which we didn’t realise till we went to remove the still unbent scaffold pole from them, when pole testing our focus has always been on the end we’re adding the weight to ! We must remind ourselves that if a pole is removed from the test rig just before it fails it wouldn’t normally return to “perfect straightness”, the scaffold pole did, therefore it’s safe to assume that it would have taken significantly more load before failing. The maximum load we put on the pole was 42.5Kg, with a leverage of approx 8.7 to 1 (distance between the wall brackets to the free length of the pole) that’d be the equivalent of about 370Kg of force on the T, that’s over a third of a ton, thus explaining why it bent
For full results see the test results table. Also see sleeving a 1.5" pole into a scaffold pole to extend it.
I suspected the test brackets might take a bit of a hammering so I’d placed a support pole (removed in the pic) under the K [the K is effectively pushed down and the T pulled up] and used a sleeve anchor on the bottom of the “extended T” (see bottom of the latter in the picture). With the benefit of hindsight I should have installed a wall anchor a few feet above the T and wedged a pole between that and the end of the T to stop it moving upwards….
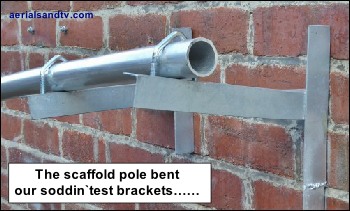
Extruded aluminium v welded aluminium poles
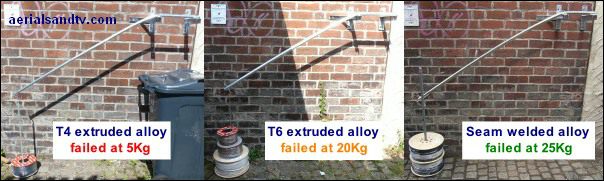
I had heard that extruded alloy poles were weaker than seam welded ones but because we only ever stocked seam welded I never gave it much thought. I was told this disparity was due to extruded alloy having a bit of air in it which would also explain why it isn’t as dense as seam welded, maybe someone out there can enlighten us whether this is true ! ? ! However, in May 2013 a mill which supplied most of the seam welded poles to the aerial industry went bust and suddenly there was a major shortage of welded aluminium poles and most of my suppliers were now offering extruded. Well, I thought, I suppose I’ll have to test them, which I did.
The first lot were T4 extruded alloy which is actually meant to be soft so it’s easier to crank. It certainly is easier to deform, it was so weak I could bend the standard 6ft x 1.25in x 16G pole over my knee. On test it failed with only 5Kg on it. Shite.
Next came the harder T6 extruded alloy, now this was much better, it failed at 20Kg.
Last I rechecked the seam welded and the weight required to fail it was exactly the same as when I tested it a few years ago, which was somewhat of a relief I can tell you. Anyway, it took 25Kg to fail which is 25% stronger than T6 extruded alloy.
I also checked 10ft x 2in x 16G poles and found the the T6 extruded poles to also be around 20% weaker than welded.
QED.
We only stock seam welded alloy poles…..
How strong are our plate mounts ?
Well the title just about covers it all I’d have thought ? When we started stocking plate mounts (sometimes called satellite mounts or patio mounts) in December 2015 we were interested to know just how strong they are. We stock them in 1.25 inch (sold here) and 2.0 inch pole diameters (sold here) and I knew it’d be pointless trying to fail the 2” models. What we can be certain is they’d be much stronger than the 1.25in mount. Anyway, as you can see, the “standard duty” 1.25in x 16 gauge (1.6mm) plate mount still hasn’t failed with 65Kg on it, though to be honest I’m unconvinced it’d have taken much more ! To put that into context a 6ft x 1.25in x 16 gauge alloy pole, which is definitely a “heavy duty” aerial pole, fails at about 25Kg…..
QED the 1.25” plate mount would take any aerial or a zone 2 (approx 60cm) satellite dish with no problem at all. I’d be very surprised if the 2” model wouldn’t comfortably take a 1m dish.
Note : we only used three M8 sleeve anchors to bolt the mount to the wall because we couldn’t be arsed to fit four, but they still took the weight with nonchalant ease. As well they might with a SWL of 300Kg each !
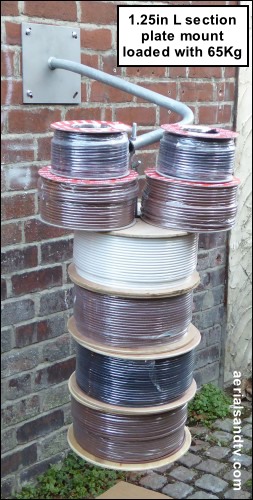