Bracket and galvanising tests : ATV's tests.
Also see ATV's poles tests
Subject list :
Brackets (and wall anchors) on test including :
- Tightening torque of wall plugs
How strong is 20mm x 20mm x 2.0mm box section alloy? incl :
- Testing the calibration of a torque wrench !
Galvanising on test incl :
- Appearance of hot dip galvanised products
- Thicknesses of zinc based anti corrosion coatings incl :
- - Pre galv v hot dip galv
- ATV “Test Tree”
- Damaged hot dip galvanising tests
- Galvanising life span
Zinc plated v stainless steel bolts corrosion resistance
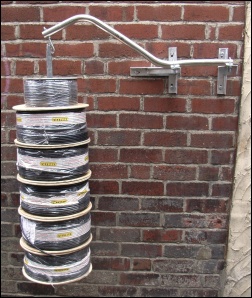
Brackets (and wall anchors) on test
Back in 2008 we undertook a comprehensive series of tests to check which poles are the strongest (alloy or steel etc), and very interesting they were, but we realised that they were also testing the 12” T & K brackets we sell, and the “Rawlplug type” (screw and plug) wall anchors. Both were very impressive.
The T & Ks obviously flexed a bit under the type of the loadings we were putting on them, but they didn’t bend that far (excluding the scaffold pole test….), and never looked anywhere near failing.
The wall anchors.....
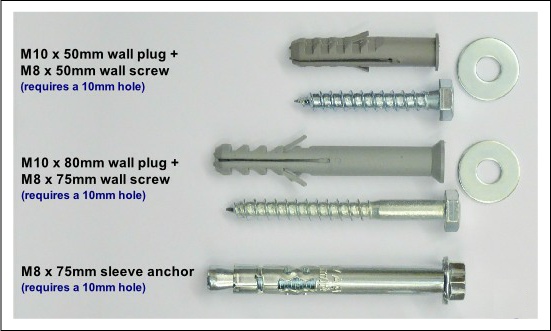
As for the wall anchors, I’ve got to say that unless your brick is soft or your hole is too big (it is essential to get a decent tightening torque on the screws) one has to wonder whether using “Rawlbolt” type fixings is worthwhile, particularly if one remembers the hole drilled in the wall needs to be bigger. You only have to look at the pictures below to see we were putting on so much load that even the strongest poles were failing, yet the “Rawlplug” type wall anchors and the brackets never showed up any deficiency whatsoever [excluding the scaffold pole tests......]. That said it must be admitted that sleeve anchors are significantly stronger than screw + plug fixings, plus the fact that the excellent performance of the screw/plug anchors was with holes only used once. When we tried reusing the same holes with new plugs (for tests at a later date) their performance wasn’t quite so impressive (we assume because the hole had been made slightly bigger ? ). Not that most people would be reusing anchor holes !
Now, it has been pointed out to me (more than once….) that these ‘tests’ of the wall anchors are only partly relevant “because they’re only being tested in shear”, not in tension, i.e. being pulled straight out of the wall as they would if the wind was blowing directly onto or off wall. However, as load is put on the pole the test K bracket will attempt to pull itself off the wall pivoting around the bottom (the T will do the opposite and pivot around the top), thus some of the anchor(s) are in tension in these tests. Always remember that the wind can act to pull wall anchors straight out so (particularly on a install with a long pole or large aerial) that should remind us that it’s important to have plenty of them in : more wall anchors = a stronger install.
NOTE : the SWL in wood (just the screws*, obviously….) is significantly greater than for the screw/plug combination in masonry. In fact in some tests I was informed about the SWL in pine (a softwood ! ) was up to four times higher than for the screw/plug combination in masonry. I expected it to be as strong, or even slightly stronger, but not that much higher, and in softwood ! It is obviously important that the screw is installed correctly (i.e. the pilot hole isn’t too big) and it’s tight, but not so tight the head of the bolt is sheared off, I wouldn’t go higher than the 15 to 20lb/ft quoted below.
* This would be for the plated wall screws, the stainless ones have a shallower thread more suitable for use with plugs in masonry. The thread is just to draw the screw into the plug to force it open and give a wedging effect, it takes no significant part in the pull out strength of the anchor. This can be proved by fact that when any screw/plug anchor fails it’s the plug which pulls out of the masonry, it’s almost never the screw pulling out of the plug.
So, when it comes to wall anchors how tight is tight ? Well we did a few crude experiments with our M8 x 50mm wall screws and their M10 wall plugs and found that 15lb/ft of torque seemed to be about right, and, very approximately, that’s putting full force about 3/4 of the way along a standard (7" long) 13mm spanner. Much tighter than 15lb/ft and you’re in danger of twisting the head off the screw or stripping the plug, then it’s a new plug needed. Stripping the plug is a pain and that wouldn’t happen with a Rawlbolt / shield anchor type fixing (or even a sleeve anchor), but it’s far preferable to splitting the brick which over tightening one of the latter may well do. If you can’t put sufficient torque on the anchor then pack out the hole (slivers of wood will do the job) until you can get decent torque on it because believe me it’s doing sod all if it’s not tight enough ! Incidentally, the recommended torque (in concrete) for our M8 sleeve anchors is only about 8 to 10lb/ft
How strong is 20mm x 20mm box section alloy ?
It’s a good job we did these tests because, at first, we were going to stock 20mm x 20mm box section at 0.8mm wall thickness, mainly, it must be said, because we could get it easily from one of the aerial manufacturers we deal with ! However it proved too weak so we had to source thicker stuff instead…
Anyway, we fabricated the test rig shown in the picture and checked how much torque we could put on the nuts before the box section bent and/or crushed. As an aside, to do this I had to bring my old torque wrench from home, but was it accurate ? It read 20% high by the way.
The 0.8mm box section crushed at less than the minimum 12lb/ft setting on the torque wrench, so we tried 1.5mm wall thickness next. That wouldn’t crush or bend even at 30lb/ft torque (though the gap was only 5mm, see adjoining picture). At that torque it was not only getting hard to hold the rig, but the wood post section was getting crushed as well. Even more significantly, the pole was being crushed despite the fact it was "heavy duty" 2.0mm wall thickness. So, why, we asked ourselves, would anyone need to go to any higher torque than this ? So we stopped at that, but, just to be sure, we decided to stock 2.0mm wall thickness anyway !
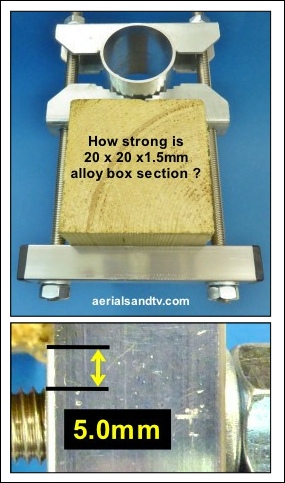
The pole was crushing before the box section alloy, and that’s a two inch pole of 2.0mm wall thickness !
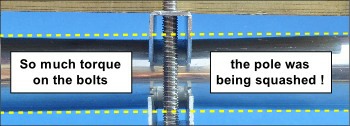
OK this was a light hearted test, but one of us put all their weight on the middle of a length of our 2.0mm wall thickness box section which straddled two tables 1.0m apart. It bent, but then more or less returned to straight ! We were impressed. Note that the weight was spread over about 1ft in the middle of the test piece, I accept a slightly more stringent test would be the weight concentrated right in the middle, but we’d already proved our point so couldn’t be arsed to go to those lengths……..
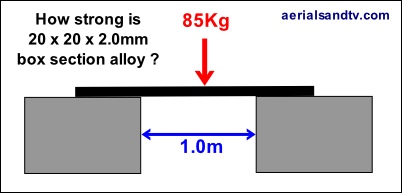
But was the torque wrench (a well used example...) accurate ?
Testing the calibration of a torque wrench : our test rig!
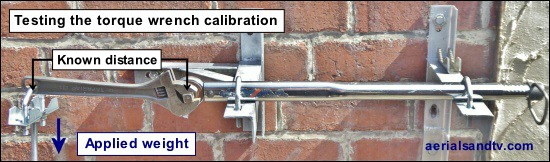
Galvanising on test
As stated on our Poles & Brackets page I really cannot understand any installer using painted brackets when galvanised are available, it really, really, really is a bodge. Well actually I can understand it. What it means is that the installer is so tight he probably needs a torque wrench to get in his wallet. He saves a quid or two, and the customer, within a year or three, gets a rusty bracket. And if the bracket’s on a light painted wall he has to repaint it every few years ! This has occurred with the install pictured on the right, coffee and cream springs to mind, which is somewhat ironic because the picture was taken at Woolley Edge motorway services (northbound, since removed) !
Basically a galvanised coating can "self heal" or “bleed over” (technical name sacrificial protection) and provide a certain amount of protection even where there isn’t much galvanising left. With painted or powder coated finishes once the corrosion gets under the paint it just spreads and brings off all the protective coating. Incidentally, do not confuse zinc passivation or plating with hot dip galvanising. The former may be a far more durable finish than painting but is not really in the same league as hot dip galvanising. Pre Galv (where metal sheet is Pre Galvanised before being formed into the component) is superior to Zinc plated (and far superior to painted), but again Pre Galv is significantly inferior to hot dip galvanising. This is particularly the case on the edges of any pre galv component where it has been stamped out, rust can start here relatively quickly because the galvanising layer is too thin to provide adequate sacrificial “bleed over” protection to the unprotected surface.

It is fair to say that plating and Pre Galv usually give a smoother and more consistent finish than hot dip galvanising, and this may be significant to some people (I don’t really know why.....). This is partly because the protection layer is quite a bit thinner in Pre Galv but also because the latter process is automated and consistent, basically a long roll of virgin clean unworked metal sheeting is unrolled, a thin layer of galvanising is applied, then it is rolled up again. But, basically, as far as we’re concerned, when it comes to galvanising, corrosion protection is the name of the game and appearance comes a long way down the list of priorities.
Remember that even damaged hot dip galavanising should still not rust, and it certainly will not spread. [link]
Typical thickness of Zinc based anti corrosion plating / galvanising :
Zinc plating = 10 microns
Pre galvanising = 20 microns (can range from 7 to 40 ! )
Hot dipped galvanising = 55 microns (45 microns)
(component up to 3.00mm)
Hot dipped galvanising = 70 microns (55 microns)
(component over 3.00mm)
Spun galvanised. These are hot dipped products which are then spun to remove excess galvanising which may fill smaller holes or required detailing, e.g. our DM Log clamp plates are spun galvanised. Although the coating is thinner than simple hot dipped it’s over twice as thick as pre galv plus the products do not have the “stamped out” (ungalvanised) edge.
Well you know what they say, a picture is worth a thousand words. The adjacent image shows a trampoline which is only 4 years old ! And it had a top cover over it every winter ! ! The springs are zinc plated and the frame is pre galvanised. Compare the poor performance of these protective finishes with that of hot dip galvanising.
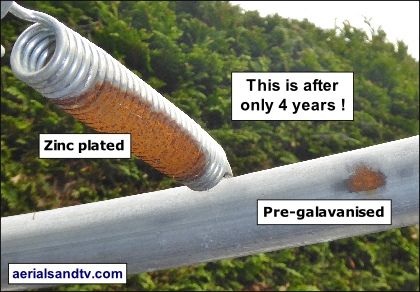
Pre galvanised V Hot dip galvanised
There is a bit more to this picture than first meets the eye. We cut off the end of each of the saddles so as to ensure there was no galvanised coating (which is much thicker in the case of hot dip galvanised) on it, though that was somewhat unnecessary for the Pre Galv item as those aren’t galvanised where they’re stamped out (of the sheet) anyway. As you can see there is no rust on the hot dip galv component, even on the exposed edge, where bleed over protection has occurred.
Obviously most components are not subject to salt water immersion (note the white salt deposits on the samples) but it just accelerates the result. At present we have a “test tree” of various hot dip and pre galvanised components outside (see below), but it will take a few years yet before the results are as clear cut as these !
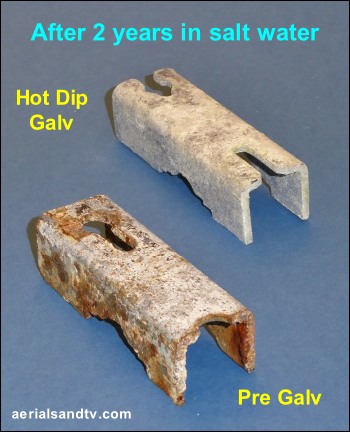
ATV test tree
Here it is, the ATV test tree, and very interesting it is too (as I’m sure you’ll all agree).
Back in 2013 we decided to start testing examples of the clamps (and saddles etc) that we sell, including with damaged galavanising / plating. Generally we file off some of the coating and/or saw off a section of the sample, although doing the latter, as stated before, is somewhat unnecessary in the case of Pre Galv products because they’re stamped out of the sheet anyway. Those exposed edges of pre galv products start rusting within a few weeks or so, as do any areas where the pre-galv has been filed off. On the undamaged items some has started to get corrosion spread (from the stamped out edge) after 3 or 4 years, in the worst cases that corrosion has spread 3 or 4mm, so far….
Some of the damaged sections of hot dip galv started surface rusting after a few years, but, significantly, it didn’t spread. None of the undamaged hot dip galv has any rust on it, nor, not unexpectedly, have any of the stainless items
A few of the zinc plated bolts started to corrode after a year or two….
Basically the test tree has just confirmed what we ’ve always said, hot dipped galvanised is far better than Pre Galv, though stainless is obviously the best.
Note the etched date in the bottom left corner, obviously all the items need that so we know how long they’ve been out there !
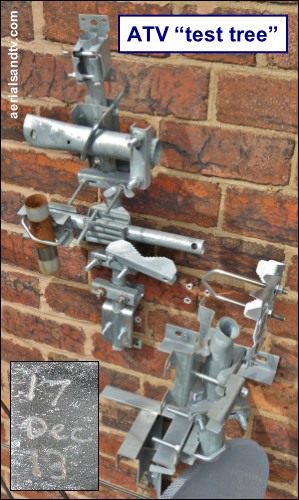
Long term testing of damaged finish on hot dip galvanised brackets.
In 2003 we set up a some experiments to monitor how hot dipped galvanising, or more accurately damaged or (slightly) imperfectly finished hot dip galvanising, maintains its anti rust properties in typical Sheffield weather. I’d be the first to admit that how quickly something rusts does depend on the area where you live, seaside locations being one the worst though heavily polluted areas are apparently worse still. Anyway, we’re no where near the sea but if we put a painted bracket with a damaged coating on our roof it starts showing rust spots within days. Not years, not months, not weeks, days........
Further interesting point, oh yes, there’s more. In the past the amount of localised pollution was the most significant factor affecting the life of galvanising protection but the clean air act has diminished its significance (relative to seaside locations) in this regard ! In fact there is a direct relationship between the corrosion rate of zinc (the protective component in galvanising) and atmospheric levels of sulphur dioxide and levels of the latter have dropped considerably since the 1970s*, thus galvanised products last longer now than they did at one time.
* I’m not an expert in this field but I would think one of the main reasons for this would be the fact coal and oil power stations had to be fitted (at great expense I may add) with Flue Gas Desulphurisation equipment to remove said sulphur dioxide from the power stations’ combustion gasses.
Anyway, back to the tests, here are the results :
In experiment 3 (back in 2004) we drilled a hole into a 6x6 galvanised wall bracket and placed it outside on its side so that water would collect in the aforementioned hole. As can be seen from the top picture the hole has rusted, but in 15 years outside it hasn’t spread at all.
Very impressive I’m sure you’ll agree
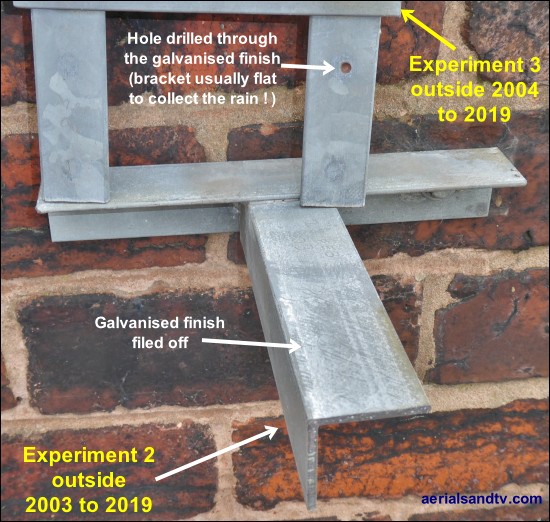
Next, in experiment 2 (Feb 2003), we tried to file off the galvanised surface on a section of galvanised "T". In 16 years it still hasn’t gone rusty.
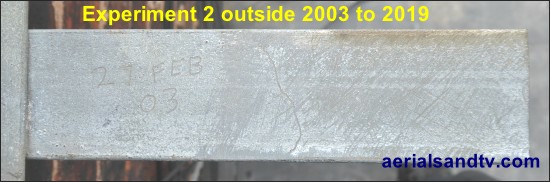
Careful inspection of the above close up picture will reveal some slight rust staining near the top edge, but that was caused by an earlier parallel experiment in which we left a painted bracket outside for a few years. Unfortunately we left the latter on top of the galvanised one and that staining actually came off the painted bracket !
Note : we’re not saying the protection on this filed off galvanising is as good as the original finish, but the fact is it still hasn’t rusted, in 16 years...…
The oldest sample wasn’t actually set up as an experiment, we just needed a lip to which we could attach an inspection light and, since we didn’t want it to rust we cut off a section from a galvanised "T" bracket and screwed that to the wall. We didn’t date it but it must have been done pre 2002, so, since the picture above was taken in 2019 it’s been out there for 17 years. As you can plainly see, although there is a small amount of rust on the cut surface, BUT it hasn’t spread at all, which is the main thing.
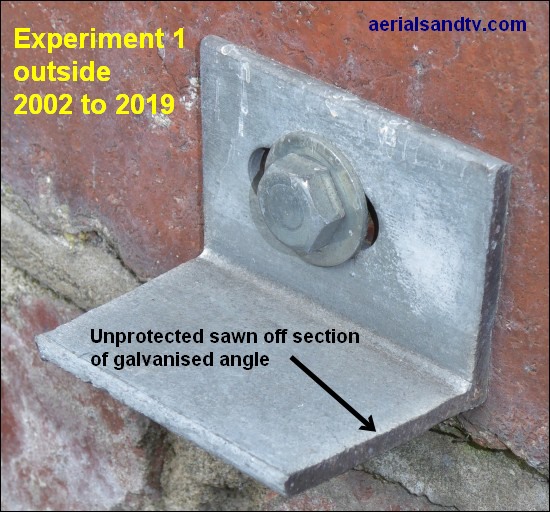
Galvanising life span
In the year 2000 the Galvanisers Association created the Zinc Millennium Map which shows graphically the average annual corrosion rate of zinc [1998 to 2000] around the UK. A thumbnail is shown alongside and the original is available on their website. The Galvanisers Association also give a post code based estimate of zinc corrosion rates (down to 10 square Kms) on the same page.
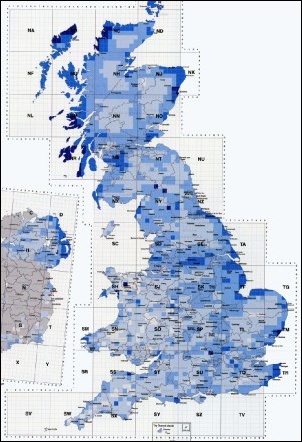
Zinc plating v stainless corrosion resistance
Before we go any further, I’d better touch on stainless steel grades. Most stainless steel nuts bolts and washers sold in this country are either A2 / 304 grade or A4 / 316 grade. In terms of corrosion resistance the former is out performed by the latter, in fact A4 grade is often referred to as “marine grade”. The down side is that A4 is more expensive though, it must be said, that for the vast majority of uses A2 stainless is fine. A2 stainless is certainly leagues ahead of the next best alternative (for most nuts and bolts) Zinc plating. The latter really is pretty poor, particularly in exposed locations, like on a clamp above your house for instance ! In fact on a decent quality install the Zinc plated V bolts will always be the first things to rust.
One does sometimes find metal components which are stainless, even A4, but they still have streaks of rust on them. I'd often wondered why, until I looked closely at some old stainless V bolts I'd adapted for a job which, critically, had required cutting for the purpose. The small amount of rust was only on the cut ends, not anywhere else. Thus, I concluded, it was fragments of the steel from the hacksaw (used to cut the bolts) that had embedded themselves in the stainless and rusted. What I have since read on this subject confirms my conclusion about my "discovery" !
I’d often wondered just how much better stainless steel is than zinc plating in terms of corrosion resistance terms. So, July 2014, I set up two tanks, one with water in it and one with salt water. Into them I placed various nuts and washers in stainless steel (A2 and A4) and with a zinc plated finish. Below is a picture of the components (out of the salt water tank) after three months, though it must be said one of the plated washers started showing signs of rust within 6 weeks. By way of comparison, in previous experiments I’ve put in un-plated screws and they started rusting within 24 hours. Rather surprisingly the plated components in the (non salt) water tank were nearly as corroded as in the brine. As and when I’ve got time (and there’s anything to report ! ), we’ll revisit these tests periodically in the future !
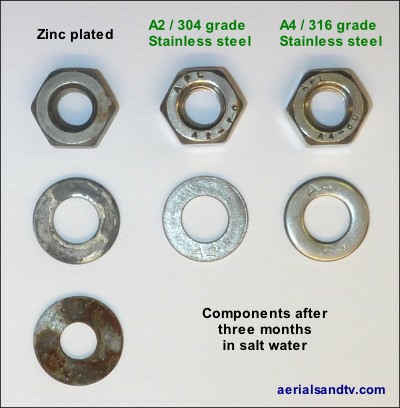
The picture is fairly self explanatory.
There looks to be a small amount of discolouration on the A2 nut but you’ll have to take my word for it that that is just the lighting !
The plated nut is rusting, you just have to look closely. All the plated components looked a lot worse before I cleaned off the rusty water on them for the photograph.
In these kind of tests it always surprises me how much difference there is in the corrosion of supposedly identical Zinc plated components, as in this test for instance. But the fact is I don’t think it’ll be long before the middle plated washer is rusty as opposed to greatly discoloured…..
Just out of interest we put a hot dipped galvanised bracket in the salt water bath and after the same 3 month period there was no rust on it. Discolouration yes, but no rust. After 15 months there was rust on the (deliberately) cut off end of the bracket, but it hadn’t spread.